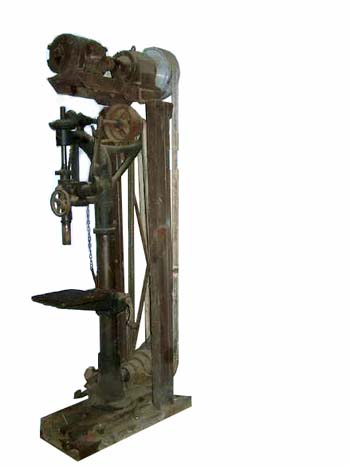
Some stuff might be hanging in the back of your mind for years and then because of a trigger things start rolling along. This is wat happened in regard to this flat belt driven drill press. I ocassionally looked on the Internet for old drill presses to see what is for sale....
Then one day I saw this drill press for sale on the Internet. The person selling the drill actually lived in the same village about half a mile away! I made an appointment to have a look at the drillpress and after agreeing on a price I could start thinking on getting it home.
As can be seen on the picture the drill was mounted inside a frame which supported the overhead motor and reduction transmission (10:1).
The manufacturer of the drill press was H.J. Reesink & Co based in Zutphen the Netherlands.
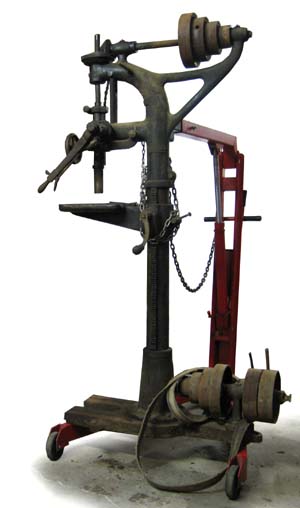
It had been in the shed of the previous owner for years and we disassembled the drill press from the motor frame. The motor assembly and the drill press was then carried to my trailer. At home the drill press was lifted from the trailer as shown on the picture on the left.
There was a lot of old grease, dirt and rust build up over the years on the machineparts. In order to get it working properly al this had to go.
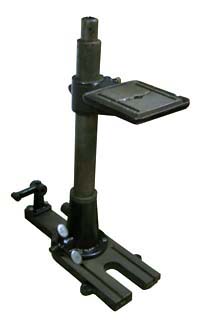
The drill press was then disassembled to get it into the workshop. Before assembling, the parts were first cleaned. If the part was originally black (a sort of tar paint) it was repainted.
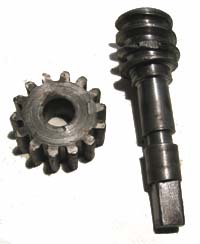
In the drill table can be lifted with the worm and gear shown. As can be seen part of the worm thread is missing and if you look closely the gear had a tooth replaced. It must have been locked up badly in the past. I left it like that since it does work properly.
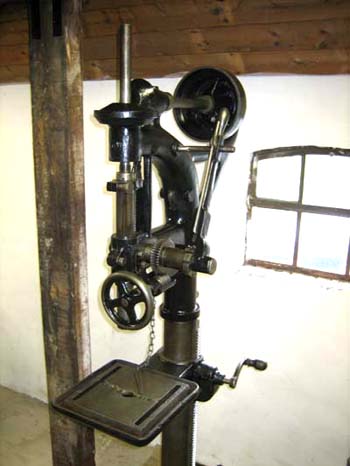
Here you can see the finished result of the cleaned and repainted top of the drill press. The axes with the flat belt wheels were heavily worn out so they were replaced with new axes made of a proper quality of steel.
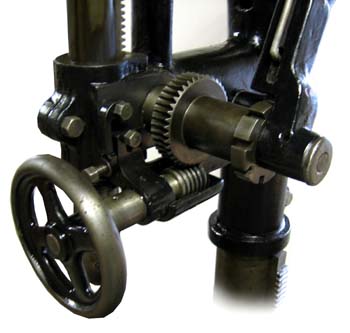
The drill feed mechanism is as usual for this type of drill press (of early 1900). It has a manual lever and a worm driven precision feed.
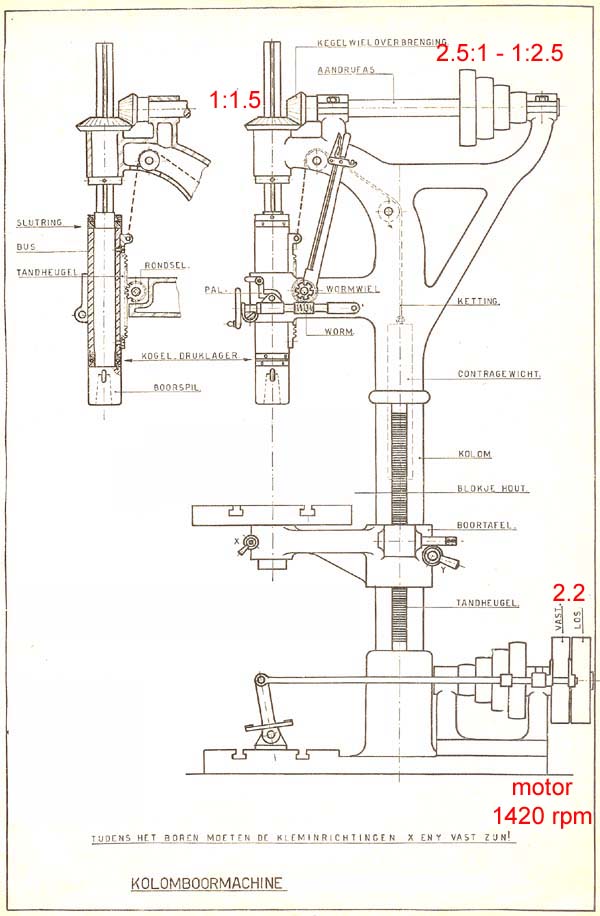
To the left you a general schematic of an early type drill press.
In the diagram the reductions are included in the picture. This way I could calculate the needed reduction for the electric motor in order for the drill to run 100 till 1000 rpm.
With a calculated reduction of 2.2 the drill will run between 170 and 1000 rpm. The wheel on the drill facing the motor is 22cm. With a reduction of 2.2 the motor will need a wheel with a diameter of 10cm. This is still acceptable for the type of flat belt that I am using.
Drill speeds are determined using the following formula: RPM=(CSx320)/D where RPM is the drill speed in Rounds Per Minute. CS is the cuttingspeed in meters per minute and D is the drill diameter in milimeters. For cutting in mild steel the maximum cuttingspeed is 21 m/min. An RPM between 170 and 1000 indicated a drill range in mild steel from 6 to around 40mm can be supported.
When I bought the drill press it had the overhead frame with a total reduction of 7.5. Therefor the drill did run between 50 and 300 RPM in the original setup. A bit to slow for me.
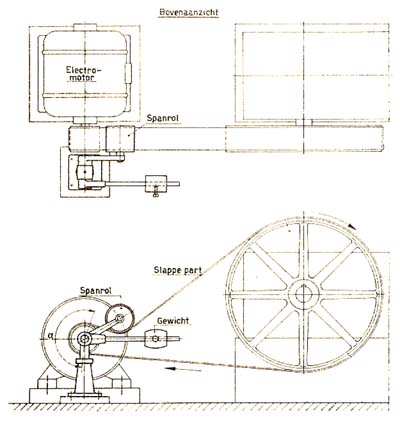
In later years the drill presses were converted to electric power using a 3-phase electric motor. On the left a schematic of such conversion. The advantage over the often found conversions using V-belts is that the pedal mechanism to move the belt from the free running wheel to the fixed wheel can be maintained which means that no modification has to be done to the drill press. On this drawing the belt is tightened using a spanner which prevents the belt from slipping.
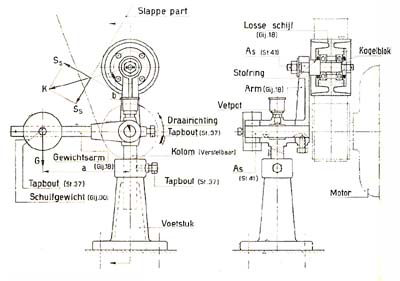
To the left the construction of the belt spanner. My first setup will be without the spanner however.